Vacu Braze is CLOSED until 7:00 AM EST

Honeycomb Brazing
March 29, 2018
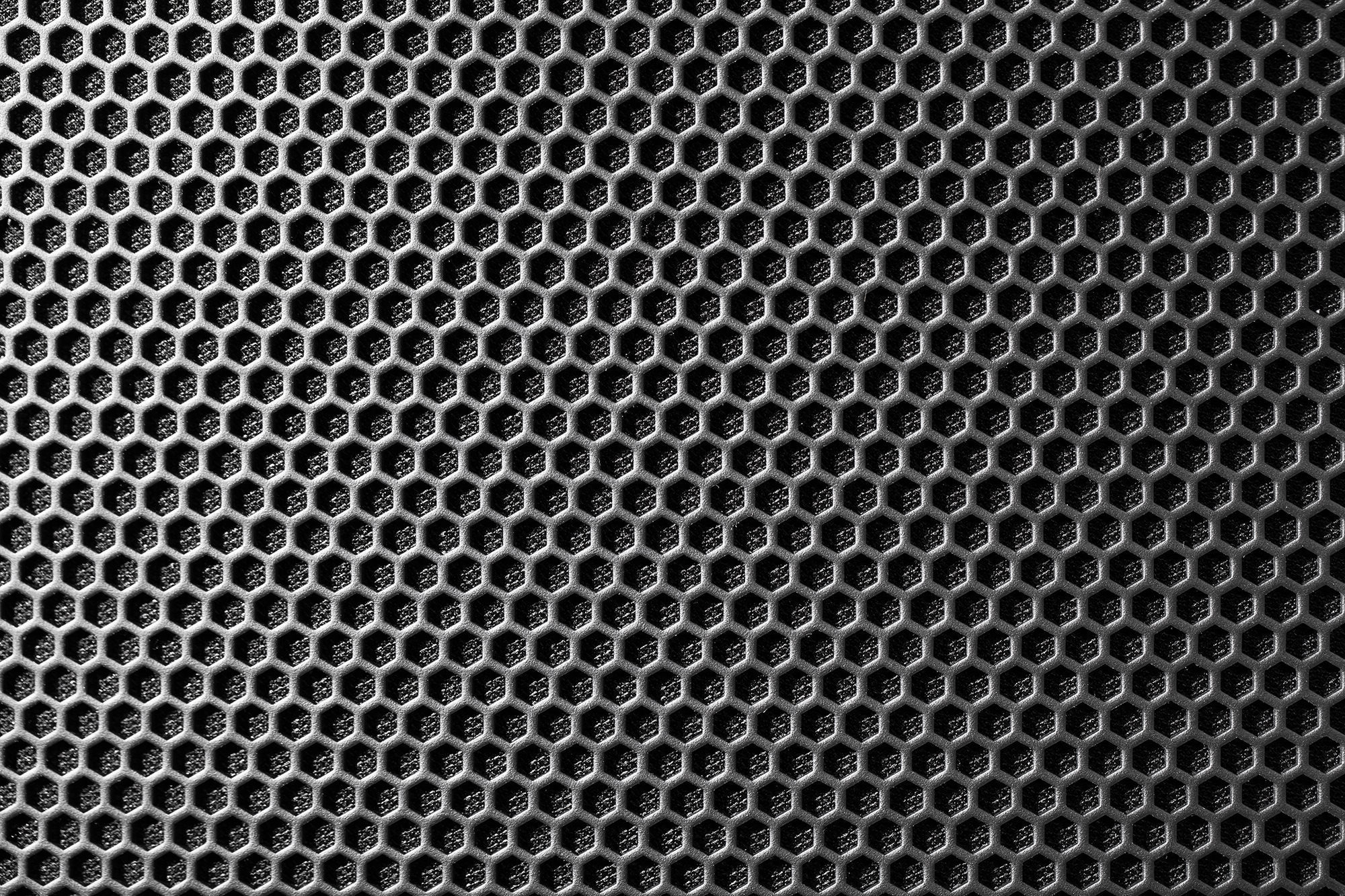
Vacu Braze offers precision brazing expertise to the aerospace and power generation industry in many avenues. They receive seal assemblies with a honeycomb surface, these seals are typically used inside jet engines like the ones that provide propulsion for passenger jets. These same seals are used to generate power inside a gas turbine. The full assembly is used as a gas seal for both the high and low-pressure turbines. However, honeycomb structures are used for a variety of applications such as train doors, aircraft bulkheads, floors, and ceilings. The design is practical due to its strength and low weight.
These structures are designed not only to be gas seals, but also a strong wear surface. So the material of the wear surface must be something that is highly resistant to many conditions that can cause failure in other steels. These are typically superalloys like Hastelloy X, and Haynes 214. Their chemical composition allows them to resist most conditions such as corrosion or overheating. Temperature resistance is essential in a wear surface due to continuous contact between two opposing surfaces, while corrosion resistance is essential to keep the piece functional and intact. These superalloys do not deform and hold the tight allowances permitted to the seals.
Vacu Braze processes all of its honeycomb brazing inside of a vacuum furnace and to a specified process. It entails joining the honeycomb surface to a base structure or backing ring to be used as a gas seal. These processes pass or exceed the qualification testing from various turbine manufacturers. In addition to this, each part benefits from being processed under vacuum. So the part comes out bright and with minimal surface distortion, staying within the tolerances allowed to the piece. Vacu Braze is constantly working to improve and expand our brazing operation.